*Sponsored content
Sustainability is no longer a mere buzzword in today’s manufacturing lexicon. It’s become a significant factor in both consumer and industrial purchasing decisions in many markets. The automotive industry is no exception.
Statistics reveal a compelling narrative: 66% of consumers now consider sustainability as one of their top five drivers behind a purchase decision. This shift in consumer mindset is propelling the industry toward a greener future, where the focus is on more than just the engines and exteriors. Designers are actively reimagining the materials that grace a car’s interior.
The journey toward sustainability in the automotive sector has been long. Historically, the industry has leaned heavily on processes that were less than kind to the environment, using vast amounts of energy, metals, plastics and other resources. But it’s no longer a niche endeavor – sustainability has become a central focus in the development of new vehicles. This reflects a deep-seated commitment to creating products that are as kind to the planet as they are to the consumer.
And as consumer preferences evolve and regulatory landscapes tighten, there’s been a noticeable shift. Gone are the days when ‘recycled plastic’ was a novel feature in a car’s interior. Now, it’s an expected standard, a baseline from which manufacturers strive to innovate further. They seek to move beyond mere compliance to embody a genuine commitment to environmental stewardship.
Beyond the 100% natural myth
Nonetheless, the path to achieving sustainability in automotive interiors is not as straightforward as replacing all traditional materials with entirely natural alternatives. A common misconception is that ‘going green’ equates to the complete elimination of plastics and synthetic materials in favor of natural materials.
OEMs are actively exploring the use of bamboo, cork, hemp, kenaf, rice hulls, agricultural waste from food crops and more in their interior parts and fabrics. In several cases, parts and fabrics made from these materials are successfully incorporated into production – but not without a critical addition.
Why? Because the reality is more nuanced. While we’ve seen a significant shift toward sustainable materials, a certain proportion of plastic remains essential to achieve things like functionality and performance in automotive parts.
In reality, integrating these organic materials with plastics is often the only way to ensure they achieve required properties. For instance, Ford undertook a recent initiative to incorporate olive tree waste with polypropylene for footrests, which need both performance properties and aesthetics. Its prototyping program highlighted the need for a balanced approach to achieve both sustainability and functionality. Ford’s team experimented with different ratios of waste material and plastic to find the combination with enough strength, durability and flexibility to replace the all-plastic version. Sustainability without trade-offs is the key.
Redefining green
The market today is witnessing a surge in the use of innovative, sustainable materials. Kenaf, a fast-growing plant, is one of the leading options. When combined with polypropylene fibers, kenaf helps remove significant weight from automotive parts. Luxury manufacturers are also experimenting with vegan ‘leathers’ derived from grapes, while sustainably harvested rattan is now used for floorboards and dashboard trim.
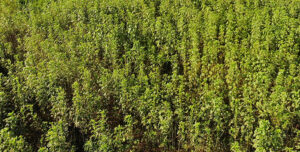
Each of these eco-friendly materials still requires plastics to enhance performance and durability. In addition to their commitment to choosing eco-friendly materials, OEMs must also ensure these materials meet the exacting standards of automotive manufacturing.
Material suppliers are stepping up to the sustainability challenge with automotive plastics that redefine the term ‘green’. For example, companies like Covestro are innovating with polycarbonate to produce versions with a lower carbon footprint, offering practical, sustainable drop-in solutions.
As a materials distributor, Formerra works with Covestro and other sustainable plastics suppliers such as Danimer and PureCycle, and then connects with compounders who can combine these materials to create specialized sustainable solutions. This type of plastics engineering expertise is crucial in the automotive space, as auto makers continue to explore unconventional materials.
A Look Ahead
The 2030 goal that several auto makers have set appears ambitious yet attainable – automotive interiors composed of nearly 100% sustainable, high-performance materials. This vision underscores the ongoing research and experimentation within the industry, as manufacturers seek eco-friendly materials that align with the principles of a circular economy.
Clearly, the narrative of sustainability in automotive interiors is evolving. It’s a complex but rewarding journey that challenges the industry to rethink its materials and processes.
For those eager to delve deeper into the intricacies of this topic, Formerra’s Automotive Interior Trend Report offers a wealth of insights into the sustainability trends and innovations shaping the future of automotive design.
As the auto industry continues to navigate the path to a greener interior, these key factors will spell success – innovation, balance, and a deep understanding of material science.
About Formerra:
Formerra is a preeminent distributor of engineered materials, connecting the world’s leading polymer producers with thousands of OEMs and brand owners across healthcare, consumer, industrial and mobility markets. Powered by technical and commercial expertise, it brings a distinctive combination of portfolio depth, supply chain strength, industry knowledge, service, leading e-commerce capabilities and ingenuity. The experienced Formerra team helps customers across multiple industries to design, select, process and develop products in new and better ways – driving improved performance, productivity, reliability and sustainability. To learn more, visit www.formerra.com.