Two research projects undertaken by Lignin Industries — the Swedish developer of Renol, a bio-based thermoplastic derived from lignin — have the potential to significantly benefit the automotive industry. Dr Christopher Carrick, founder and CTO of Lignin Industries and Dr Lars Jerpdal of Scania presented details of the initiatives at a recent industry event.
Renol can be used in polypropylene (PP) and acrylonitrile butadiene styrene (ABS) for thermoforming and injection molding. It reduces the CO2 footprint by replacing fossil-based plastics and enables nucleation for the Ku-Fizz process, which produces lightweight parts to reduce CO2 emissions even further. As a result, Renol is a promising option for meeting the ELV Directive.
The first project, called Bioform, aimed to develop vacuum-formable materials to replace fossil-based plastics with bio-based alternatives. This was achieved by incorporating a high bio-based content into ABS. According to Lignin Industries, results show that the bio-materials developed represent a major breakthrough for the automotive sector, offering a sustainable alternative to traditional fossil-based materials.
Project stakeholders alongside Lignin Industries include Vinnova (the Swedish government’s innovation agency), Scania, AutoForm and KTH Royal Institute of Technology.
The project successfully replaced up to 44% of plastic content with bio-based fillers, resulting in a 40% reduction in carbon footprint. The bio-based materials demonstrated enhanced fire retardancy, improved mechanical performance and notable environmental benefits, making them highly suitable for various automotive applications, including interior trims, exterior parts, dashboards, door panels and roof boxes. Additionally, lignin-based plastics showed good processability for extrusion and vacuum forming.
The study concluded that the reduced carbon footprint profile of bio-based materials like lignin makes them a promising solution for the automotive industry’s sustainability goals. This is especially important as the industry pushes to reduce reliance on fossil-based materials and achieve significant cuts in greenhouse gas emissions by 2050.
Read the end-of-project report here.
Project two focuses on Ku-Fizz, an economical microcellular injection molding technology originated by Volkswagen Group, which produces lightweight automotive parts.
During the Ku-Fizz process, a nucleating agent is needed to form the microcellular structure by providing a surface for the gas to attach to and grow from. Traditionally, glass fibers have been used for this purpose. However, the stiffness and lack of flexibility of glass-fiber-filled plastics make them unsuitable for some applications. To address this, Lignin Industries developed lightweight injection-molded products using Renol as a foaming activator and CO2 reducer.
The project found that using Renol as a PP nucleating agent led to several breakthroughs. It achieved a 10% weight reduction compared with unfilled injection-molded PP, along with a 30% reduction in cycle time compared with traditional injection molding. Additionally, it reduced the clamping force by 70%, allowing for the use of a smaller injection molding machine. Unlike glass fibers – commonly used in the Ku-Fizz process but prone to deterioration after the first cycle – Renol can be reprocessed repeatedly without losing its properties. Moreover, Renol provides isotropic properties, making it easier to achieve flat surfaces, which is essential for widespread industry adoption.
When used in the Ku-Fizz process, Renol reduces the carbon footprint of the final product in three ways. First, as a bio-based material, it inherently has a lower carbon footprint than fossil-based plastics. Second, incorporating Renol within the Ku-Fizz technique reduces weight, meaning less material is needed. Finally, the decreased weight also results in lower CO2 emissions during the use phase (Scope 3) for the automotive industry.
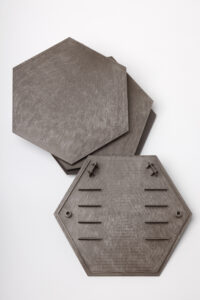
Dr Carrick said, “In looking to nature, we have found a truly sustainable and scalable bio-based plastic solution, one that can deliver major emissions reductions across industries and product categories. I thank our partners for their contributions to the projects, and I thank Scania for their vision in looking to implement some of the findings. I was only too happy to share our findings at PIAE in Mannheim and look forward to speaking to colleagues and stakeholders on how Renol can transform their supply and value chains.”