Thermoplastic resin producer Braskem and composite forming technology company Weav3D, in partnership with the Clemson University’s Composites Center, have been awarded first place in the 2024 Altair Enlighten Award’s Future of Lightweighting category.
The awards honor the greatest sustainability and lightweighting advancements that successfully reduce carbon footprint, mitigate water and energy consumption, and leverage material reuse and recycling efforts within the automotive industry. The 2024 awards were presented at the CAR Management Briefing Seminars on August 6, 2024.
The project, which builds on Clemson University’s expertise in thermoplastic composites gained in the US Department of Energy’s Ultra-Lightweight Door program, has resulted in the development of an industry-first high-rate structural automotive prototype.
The awards recognizes the companies’ Rebar for Plastics lattice technology, which combines Braskem’s polypropylene (PP) sheets with Weav3D’s composite lattice system to create high-strength, lightweight materials for structural and automotive applications.
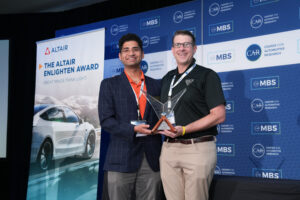
Christopher Oberste, president and chief engineer of Weav3D, said, “This award validates the technical development and commercialization progress we have achieved over the past several years and recognizes the importance of Weav3D’s cost-effective lightweighting technology as part of the future of sustainable mobility.”
The Rebar for Plastics technology is designed to be a cost-effective and sustainable alternative to traditional materials used in vehicle manufacturing. By integrating Weave3D’s lattice reinforcement with Braskem’s PP, the team has developed a lighter and more economical thermoplastic solution compared to conventional organosheet that it says unlocks new opportunities for creating a replacement for sheet metal structures with thermoplastics in vehicles.
Joel Carr, technical service and development engineering team leader at Braskem America, said, “The partnership between Weav3D, Clemson Composites Center and Braskem combined to create a truly innovative material that provides for more sustainable lightweight solution to help reduce vehicle carbon emissions all while enhancing manufacturing process value through material cost savings. This is a win-win for our clients and the planet.”
Sai Aditya Pradeep, former manufacturing applications engineer and project lead for Clemson, said, “We collaborated with Weav3D and Braskem to develop an industry-first high-rate structural automotive prototype that showcases Weav3D’s tunable woven composite technology and Braskem’s cost-effective PP resin, leveraging our extensive experience in stamp-forming thermoplastic composites from the US Department of Energy’s Ultra-Lightweight Door program.”